Drone technology is a groundbreaking survey tool, but we think it sometimes steals the limelight away from photogrammetry itself. The real magic occurs post-processing, where you have freedom to explore and engage with your site in ways you never could from the ground.
For photogrammetry processing and analytics software, we get a lot of questions about capabilities on the road to commitment. A lot of, “What exactly does drone data get me that I don’t already have? What’s the ROI?”
1. Fast data processing
We’ve heard the nightmarish processing stories—days going by; computers tied up, only to crash at the last minute; starting again from scratch.
Earthwork is a complex beast because each subsequent stage depends on the success of the one before it. Not only does planning your whole day around processing displace valuable bandwidth, but it also complicates project timelines.
The time-suck of unreliable processing has plagued surveyors for too long. That’s why you should be able to lean on your processing provider for a consistent turnaround time.
When you know processing will take a fixed amount of time, you know exactly how long until you can relay flyover data to everyone who matters—managers, supers, clients all stay informed.
Photogrammetric Processing 101: To Self-Process, or to Not Self-Process?
2. Cloud-based access
Imagine this scenario: you’ve finished your flight, you have all the aerial data you need, and you’re far from your home-base desktop computer in the middle of nowhere.
Do you want to wait two days until you’re back in the office to process your data? Or, do you want to connect to your site WiFi or hotspot, log on to a portal, and upload your data for processing right then and there?
With the cloud-based drone software, you can upload anywhere you get a signal. Look for solutions that make it easy to drag and drop your flight data directly into the portal, select your preferred coordinate reference system, and go.
3. Interactive 3D site models
Drones have been used in surveying workflows for a decade now, but they’ve only in the past few years become affordable enough to benefit SMBs as much as they benefit larger organizations.
During a flyover, drones are snapping images of your site from above, geotagging them with location data. When you stitch all those photos together and add elevation data, what you get is a high-resolution 3D map of your site.
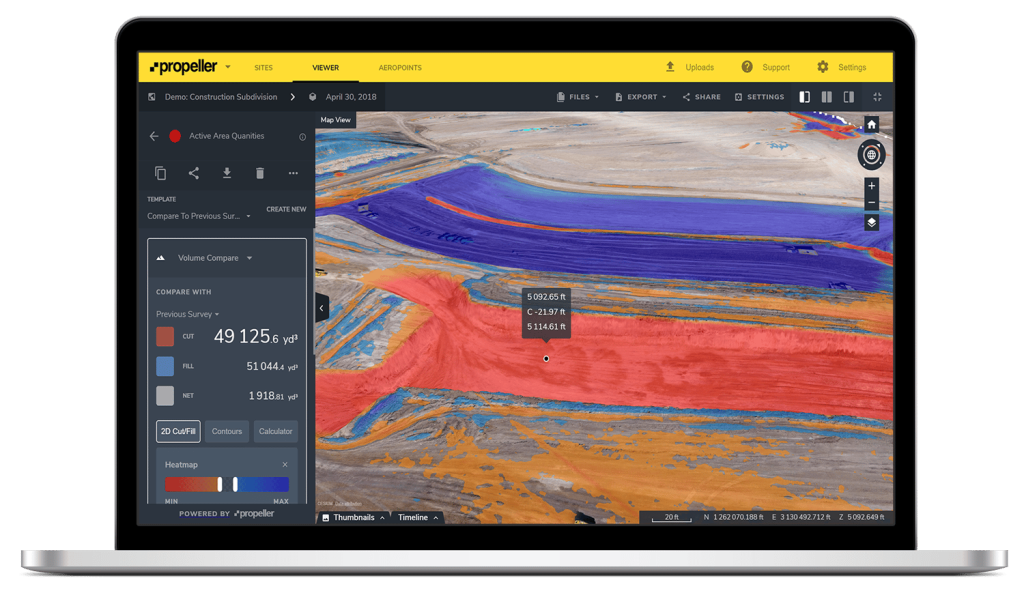
Anyone in your organization can make instant observations from photorealistic 3D models—a misplaced machine, hazardous conditions, and other points of interest you might have otherwise missed from the ground.
But more importantly, you can actively engage with your site from afar and make real-world measurements to expedite decision-making needed to keep the project moving.
The interactivity of 3D models available in drone software takes a variety of forms, which we’ll explore throughout this article.
Check out this simple five-step guide on creating 3D drone models.
4. Progress tracking powers
Because drones help you increase survey frequency, you wind up with a comprehensive visual record of on-site activity. With multiple surveys, you can start comparing your material movement progress over time. You can also take a single dataset and layer it against design plans to determine how far you have left to go.
If you choose to fly before you dig, when development is in its infancy, you can integrate visuals into the planning process. This is just one of the ways our friends over at Haydon Materials, a quarry and aggregates company, apply their 3D visuals.
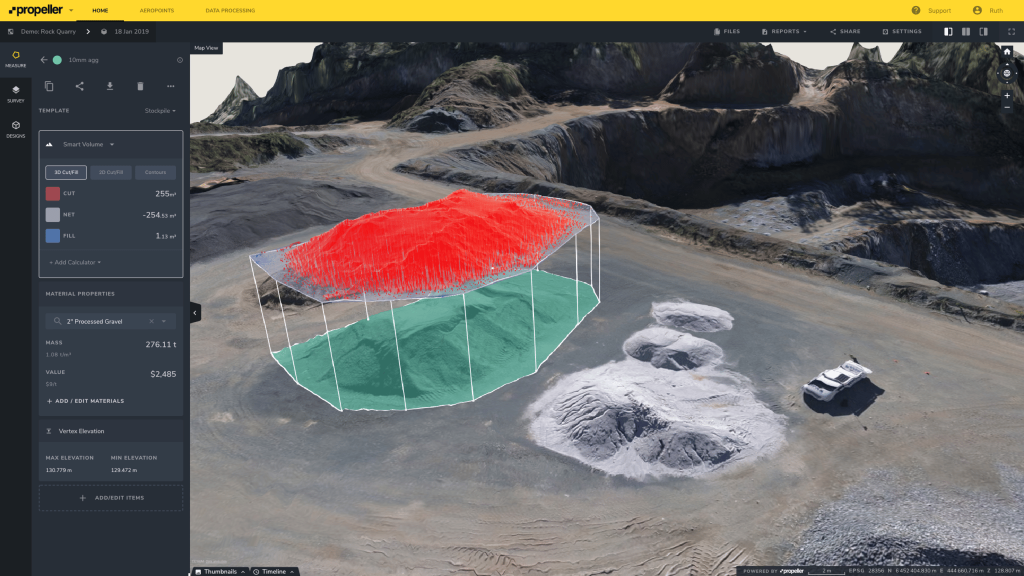
“We’ll fly an entire site, put a layout on it, and show our operations managers how to approach the mine and which direction to go,” explained Haydon.
While on the surface, they’re using drone software just to plan jobs more effectively, they’re also keeping everyone involved in the project informed to reduce error and tame conflicting expectations.
Kentucky-based Haydon Materials Uses Propeller for Quarry End-of-Month and More
5. Risk assessment capabilities
Naturally, with new visibility comes new perspective. Apart from tracking progress, you’re also pinpointing safety risks and constantly assessing risk. Each year, there are roughly 150,000 construction site accidents that result in injury.
You have to wonder how many of those could have been prevented with the objective lens 3D site models offer up. Using an aerial vantage point, you’re able to actively assess risk and clean up problem areas before an accident occurs.
Too often, worksites get caught in a retroactive state, implementing processes and preventative measures after an incident happens to decrease the opportunity for recurrence.
With continuous self-auditing, you can build a proactive environment that keeps everyone onsite safe.
6. Interactive measurement toolbox
Exploring your worksite in 3D is interesting, but there’s so much more beneath the surface, There’s actionable data to be had that makes your day-to-day easier and more efficient. This is how ROI funnels in.
Post-survey, you’re not just receiving an aerially captured replica of your site. You’re gaining a whole new layer of visibility into your material movement.
Look for drone software that allows you to clean up terrain to remove inaccuracies or obstructions if you’re dealing with thick vegetation or foliage—correcting the visual appearance to breach a new level of layer of accuracy.
Once you’ve removed all the features obscuring your vantage point, it’s time to measure your material movement. In just a few clicks, you should be well on your way to earthwork analysis.
On-screen calculators and analysis tools make measuring volumes, surface areas, road grades, elevations, cross-sections, and cut/fill a piece of cake.
7. Evidence for conflict resolution
Almost always, disputes arise from ambiguity. Someone fails to relay a critical piece of information and the effects trickle down throughout the project.
Of course, there are other common instigators besides miscommunication—noncompliance, unrealistic expectations, insufficient documentation, and so on.
There’s a trickle-down quality to the benefits of 3D drone maps. If you can track site progress between flyovers and clearly communicate that progress to the people who need to know, then project-related disputes will occur less frequently.
For example, if there’s a question of where a water line should go, or how much dirt you’ve excavated, you have all that information you need at your fingertips. Blount Contracting uses the cross-section measurements for disputes like this.
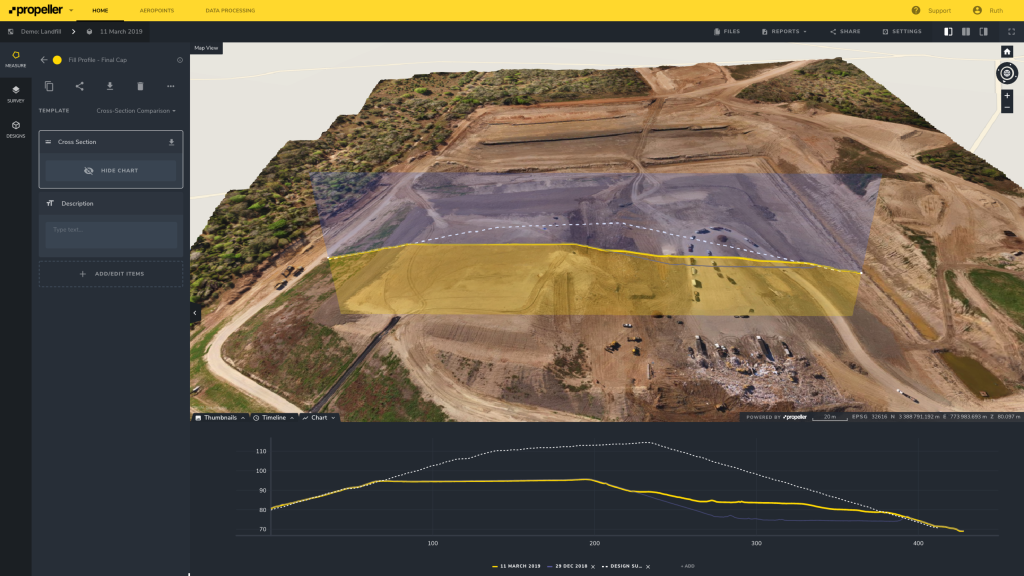
Of course, simply having more frequent project snapshots thanks to drones has its own implicit benefit when it comes to conflict resolution. The more evidence you have of your work, the easier it will be to prove to project owners you come into conflict with,
8. Cross-team collaboration
Job sites are teeming with people performing a variety of simultaneous tasks. Engineers are perfecting design documents while foremen are managing their teams. Environmental regulators might be operating in the background while subcontractors execute their niche tasks.
The measurements and progress reports you can generate from drone data software serve each of those roles in one way or another. Rather than building silos, you can keep central lines of communication open by using your 3D models as a common meeting ground for all teams. When everyone is relying on the same source of truth, there’s less chance of miscommunication and miswork.
As collaboration and cross-team communication becomes more fluid, the window for unexpected (and unwelcomed) mistakes shrinks.
Why Reporting and Collaboration Matter on Construction Sites
9. Seamless data exporting
A successful project depends on consistently getting the right (accurate and up-to-date) information in front of the right people. Your ideal drone survey software should make it easy to export everything from measurements and reports to the raw data itself.
Look for platforms that allow you to quickly customize and generate reports for specific workflows, such as stockpile management. It should be seamless to export CSVs that can be integrated into other reporting software.
10. Comprehensive worksite management solution
If you haven’t had the ah-ha moment yet, that’s okay. It’s a big decision, and every big decision should be coupled with a clear path to financial or operational gains.
We’ve deconstructed the individual features you should look for in drone data software, but the big picture is that it should have the ability to scale into a more comprehensive worksite management solution..
When we add up each of the nine things above and consider how they function together. What we arrive at is a one-stop-shop worksite management platform. An integrated approach to managing your progress, your project, and your people.
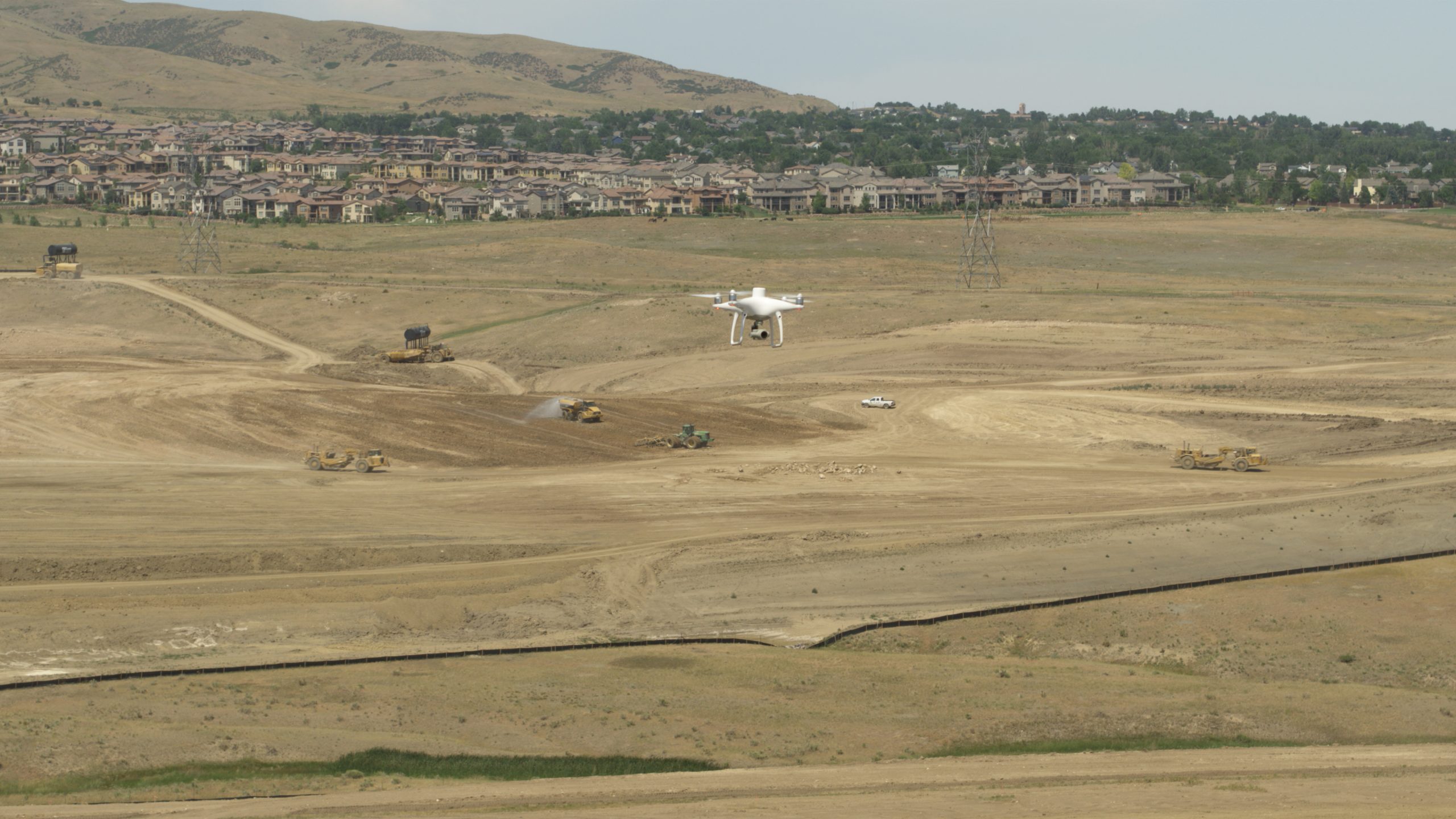
All of our customers tell us a similar story before they embraced drones—tight deadlines debilitated by data gaps, unreliable surveying schedules, disparate teams with communication silos.
And then they tell us about what life’s like after making the leap.
“If I were on a jobsite where we didn’t have Propeller, it’d be a lot less convenient and it’d take a lot more time to do things. The bird’s-eye view gives you a really good perspective of what’s on the jobsite [ . . .] and it gives you a perspective that you wouldn’t have if you were standing on the jobsite looking at things,” said Field Engineer, Maggie Porter, at Hensel Phelps.
The best thing drone survey software should get you is the freedom to leverage in-platform tools beyond their surface-value. The more insights into your worksite, the better work you can do.