We wrote this guide to cut through the confusion and get straight to what you need to know about PPK
There’s PPK and Propeller PPK. The difference? A smart and integrated workflow that makes survey data scalable. Propeller’s PPK workflow is the most efficient and accurate surveying solution for AEC professionals. In this guide, we’ll explain what PPK is, how to use it, and why it’s the industry standard for high-accuracy drone surveying.
Intro to PPK
What is PPK?
PPK stands for “post-processing kinematic,” a type of drone surveying workflow that improves the accuracy of location data by taking GPS data recorded during flight and adjusting it afterward using base station data. PPK ensures precise and consistent survey results by eliminating reliance on unreliable real-time correction signals. When you survey using PPK drone mapping, the images and GPS data collected by your drone are corrected against data from a base station post-flight rather than in real-time.
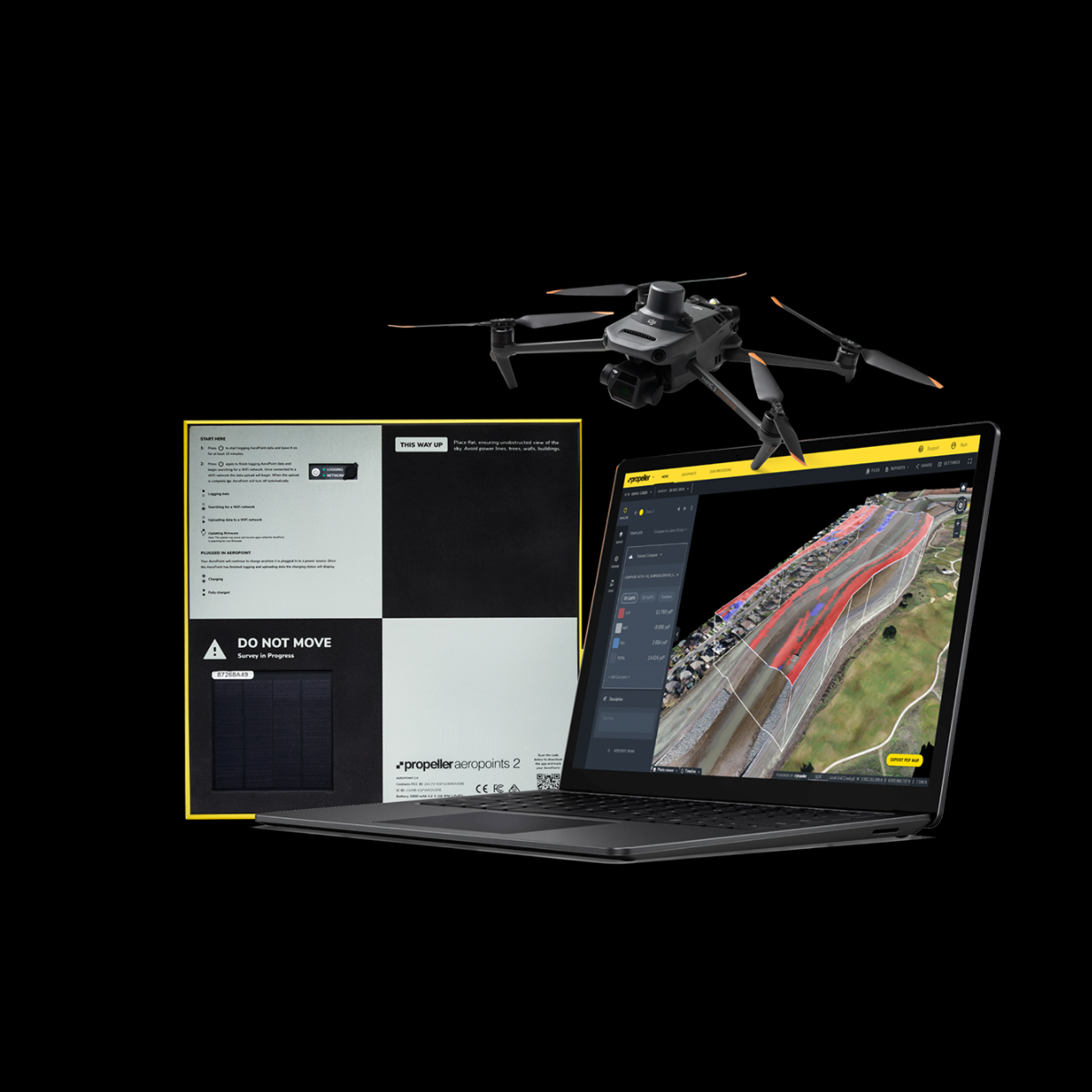
How does it work?
Collecting enough images and GPS data to create a detailed 3D map of your worksite might sound complicated, but Propeller’s PPK workflow boils down to three simple steps:
Step 1: Place your AeroPoints
Set up your ground control by placing at least one AeroPoint within your survey area
Step 3: Upload your data
Connect to wifi and let your devices upload their data to the cloud.
The role of ground control
In the pursuit of accurate data, there is no looking past ground control. Other technologies, such as onboard RTK/PPK, will provide improved accuracy in the air, but this does not automatically translate to the same accuracy on the ground.
Terrain models corrected with onboard RTK and PPK data are still more susceptible to turbulence, vibration, and camera calibration errors than models generated using ground control points.
Combined errors of ten degrees or more in a drone’s measured pitch or roll can introduce tens of centimeters of error in the final model if no GCPs are in place. With this in mind, achieving centimeter-level ground accuracy in surveys with onboard PPK/RTK is significantly more difficult without the inclusion of ground control points.
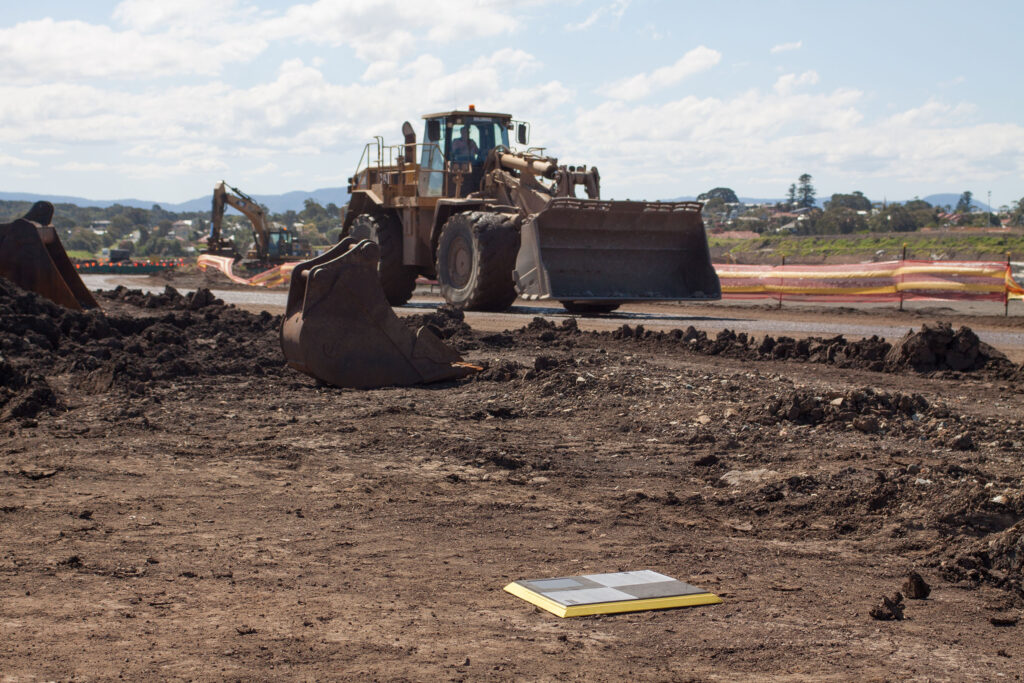
What’s happening behind the scenes?
While you fly your RTK-enabled drone, a base unit (a base station, AeroPoint, or CORS network) separately records positional information. That base unit provides more accurate triangulation than you can get from the drone alone. Post-flight, GPS data from the drone and base unit are matched using timestamps on the photos. The more accurate positional data from the base can then tie your results to known points on the ground and course-correct your drone data for precise positioning.
Because the drone’s position in the sky is not accurately geotagged, you don’t get reliable positional data from its onboard hardware alone. You need known coordinates on the ground to pin your drone images to an exact location on Earth. Absolute accuracy with GCPs can be refined to centimeters (not meters), making them the gold standard for survey-grade data.
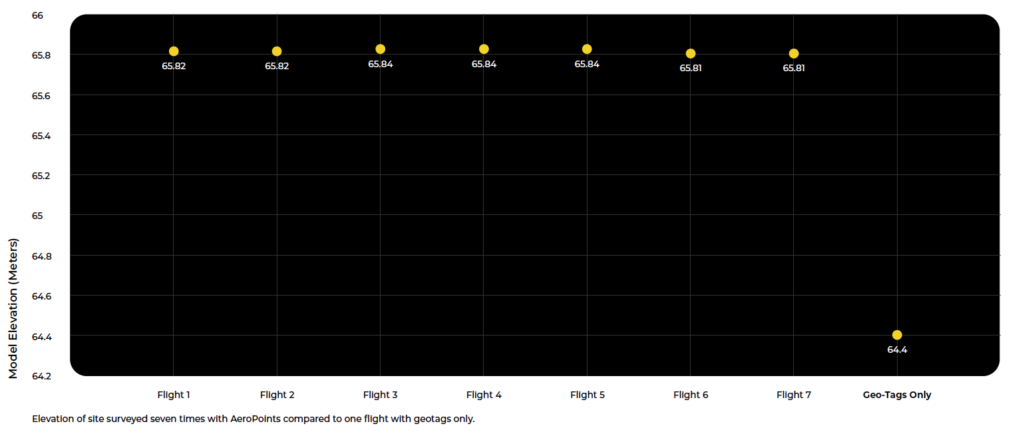
Although ground control points (GCPs) are critical to achieving high-accuracy data, they can be time-consuming and even dangerous to set up on a large worksite.
Measuring and marking them manually involves detailed knowledge of where to place them, walking potentially hazardous terrain, and re-shooting points as your site changes.
AeroPoints take all that complexity away — but, we’ll get to how those work later on. For now, all you need to know is that Propeller’s PPK workflow leverages the accuracy boost of ground control without the hassle.
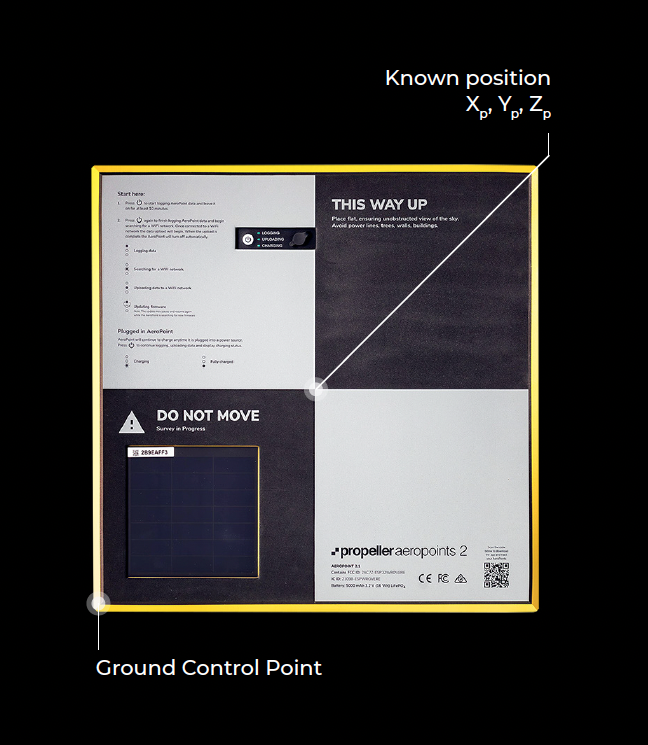
AeroPoints
AeroPoints are the industry standard for ground control and the bastion of survey-grade accuracy. Portable, lightweight, and easy to use, they provide essential corrections to correct the aerial data collected during flight.
Where traditional ground control is labor-intensive to shoot, mark, and maintain, a single AeroPoint offers the same precision as a handful of GCPs—in far less time. More than ground control, AeroPoints are a combined GCP and base station, so you only need 1–3 for sites up to 150 acres (60 hectares). However, we recommend putting one or two more down as checkpoints so you can determine surface accuracy.
Place them anywhere within your survey zone with a clear view of the sky and a relatively flat surface before you fly, and simply pick them back up when you’re done.
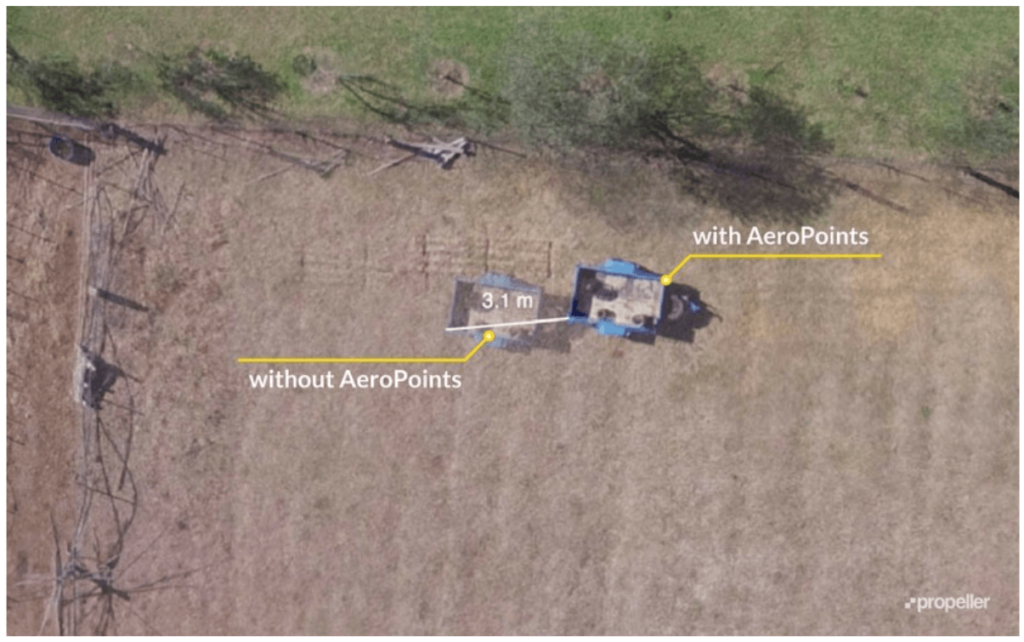
Example planar shift between data sets generated with AeroPoints and those using just onboard geotags.
High-accuracy drones
Not all drones are created equal. With a wide range of commercial drones on the market, it’s important to understand the capability of the hardware you choose. PPK requires an RTK-enabled drone that can attach geocoordinates to each image based on an onboard GNSS device.
While our list of recommended drones isn’t the end-all-be-all of PPK drone mapping, we’ve carefully tested and selected the drones that we know provide maximum accuracy and compatibility. Our list includes options for every budget, experience level, and site size.
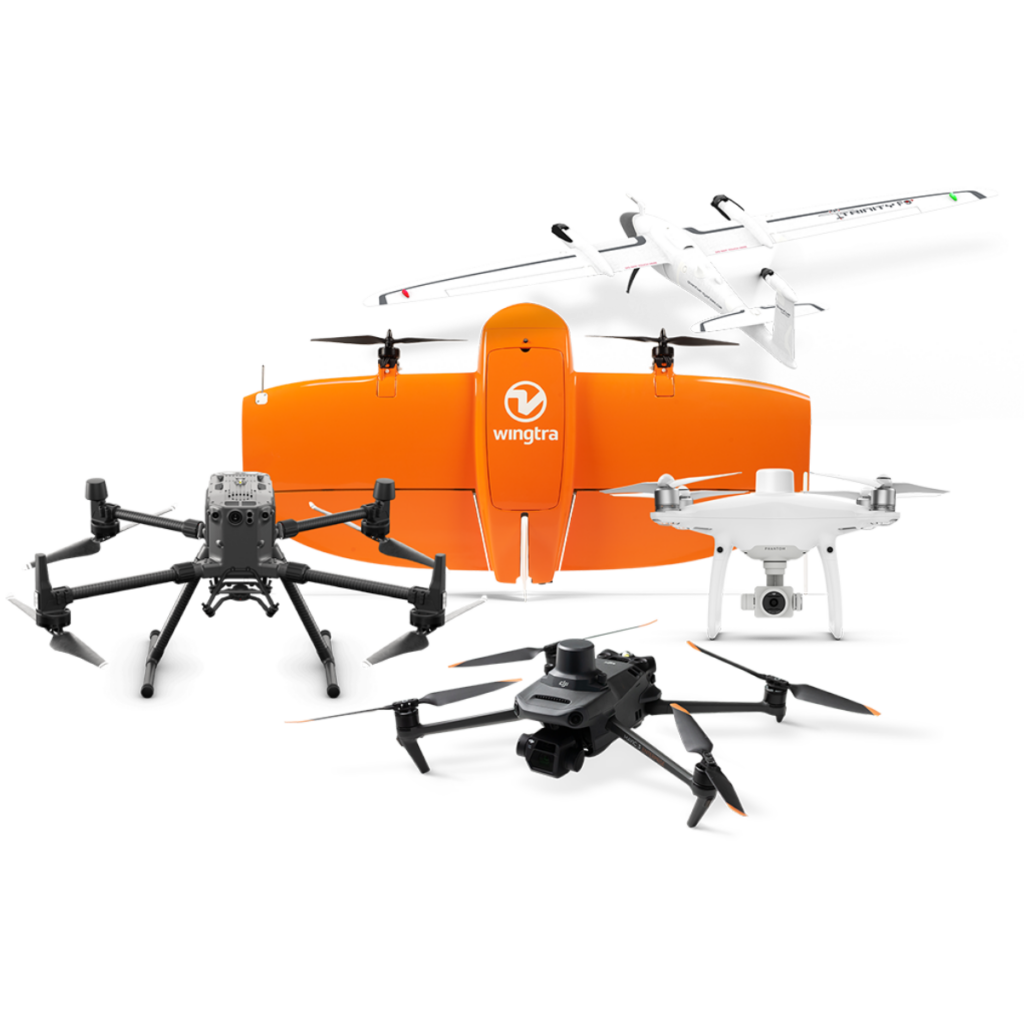
PPK Processing
Collecting aerial imagery and positional data is just the first part of creating a digital map of your worksite. The next is synthesizing all that data into a finished, measurable output: a 3D map.
The act of processing your position and orientation system (POS) data, ground control, and drone images into a single map is called photogrammetry. It’s a highly technical process requiring specialized training, robust software, and lots of computer processing power.
Propeller lets your team offload the heavy burden of managing this step in-house. No more worrying about when (or if) you’ll end up with a reliable map and actionable data. (More on processing in the next section.)
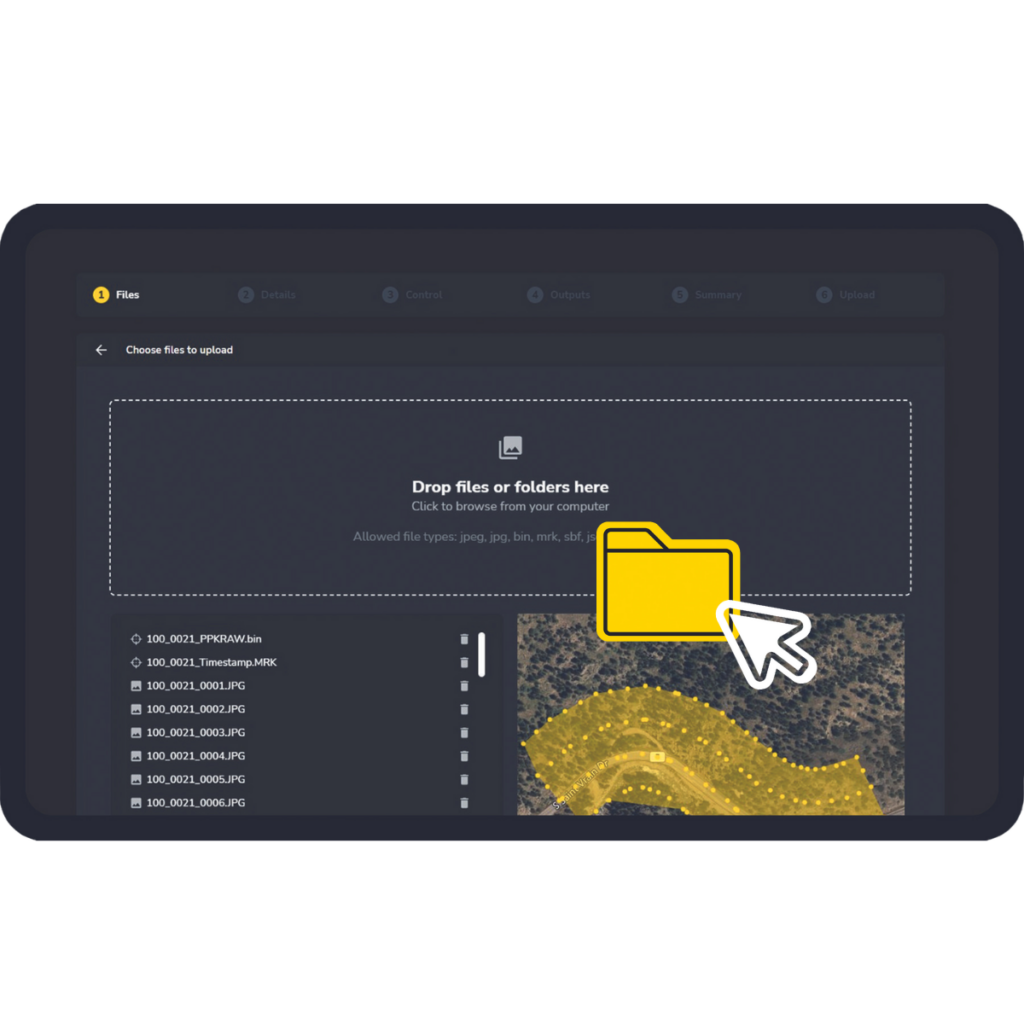
PPK vs. RTK
If you’ve done any drone surveying in the past, you’re probably familiar with RTK. Let’s quickly review how RTK works before we dig into the difference between PPK and RTK.
Real-time kinematic positioning (RTK)?
Real-time kinematic (RTK) data is a piece of the surveying workflow puzzle; we’ve already mentioned that PPK requires an RTK-enabled drone that can collect geolocation data during flight.
When we talk about PPK vs. RTK, we’re talking about RTK as a workflow. In this context, RTK means that POS data is processed in real-time through direct contact with a base station during flight.
PPK and RTK workflows both require RTK-enabled drones with onboard GNSS sensors and a base unit to operate. The main difference between PPK and RTK workflows is when that base unit’s data is processed.
PPK
In a PPK workflow, we process and correct the drone’s data after the flight has concluded. Working this way improves reliability and consistency because it means that the drone and base unit are collecting data independently, so there isn’t a risk of losing connectivity during flight which would impact accuracy.
RTK
In an RTK workflow, any loss of contact between the drone and base unit will distort your dataset. A number of factors can disrupt this connection, including turbulence, physical obstacles like trees or buildings, and unpredictable connectivity gaps. (Remember those “Can you hear me now?” commercials?)
What happens after you fly?
Laying down AeroPoints and flying your drone is just the first part of PPK’s story. So what happens to all that data once it’s been collected?
Before you can get your hands on a usable 3D map, your data must be processed. You can choose to process your data in-house or outsource to Propeller as the final step in the PPK workflow.
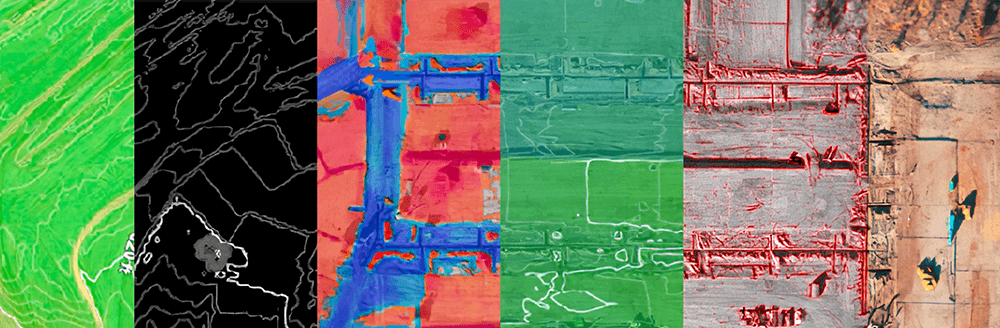
What’s involved in data processing?
Self-processing data is labor-intensive, and there’s likely just one person on your team with the software and technical know-how to do it. Working alone, it can take them days to convert survey data into a map.
Some teams prefer the hands-on approach of managing their own data during processing. But when surveyors look closely at self-processing, they often find:
- Self-processing doesn’t scale well: Processing requires trained (and often expensive) geospatial scientists and additional hardware to process more than one survey at a time.
- Huge processing power demands. A good photogrammetry computer can cost more than $10,000.
- Long processing timelines. Even with the right equipment, the computer cannot perform other tasks while processing your survey data. Each survey takes hours or even days to process, and must be done one at a time.
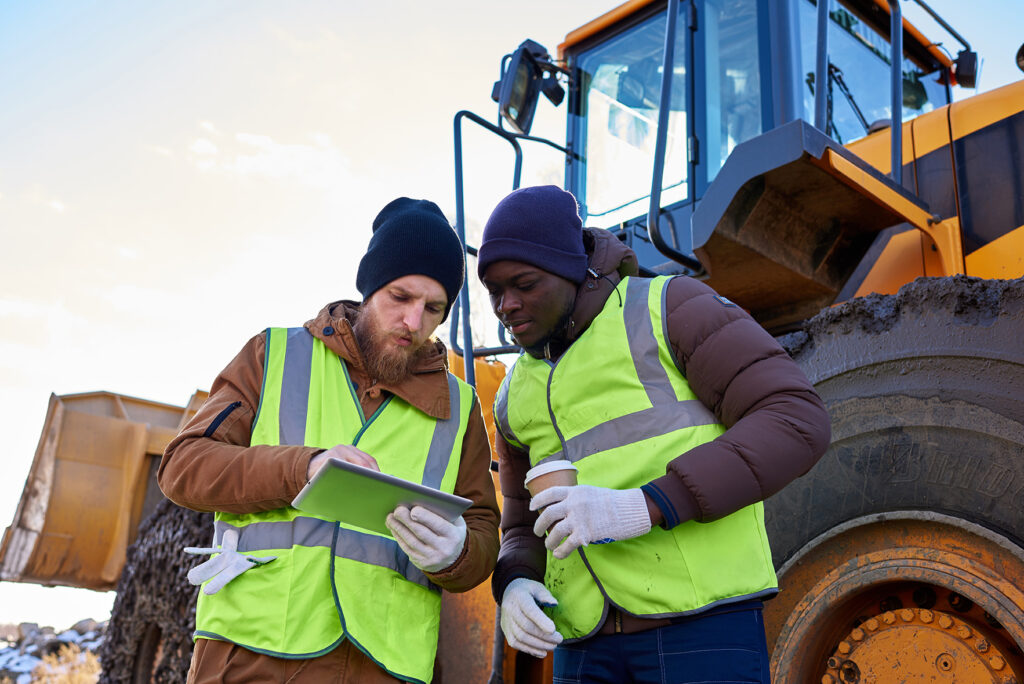
Why outsource your processing to Propeller?
It takes a lot of technical expertise to turn millions of data points into realistic and accurate 3D maps. Our survey processing pipeline is managed by a team of geospatial scientists, making accuracy repeatable and predictable, no matter how many datasets you’re juggling.
With Propeller’s outsourced solution, you’re done as soon as you upload your data. We’ll build a high-resolution terrain model, point cloud, orthophoto, and other survey deliverables in a matter of hours. We work as an extension of your survey team, using a mix of automated QA and human supervision to ensure historical consistency between datasets.
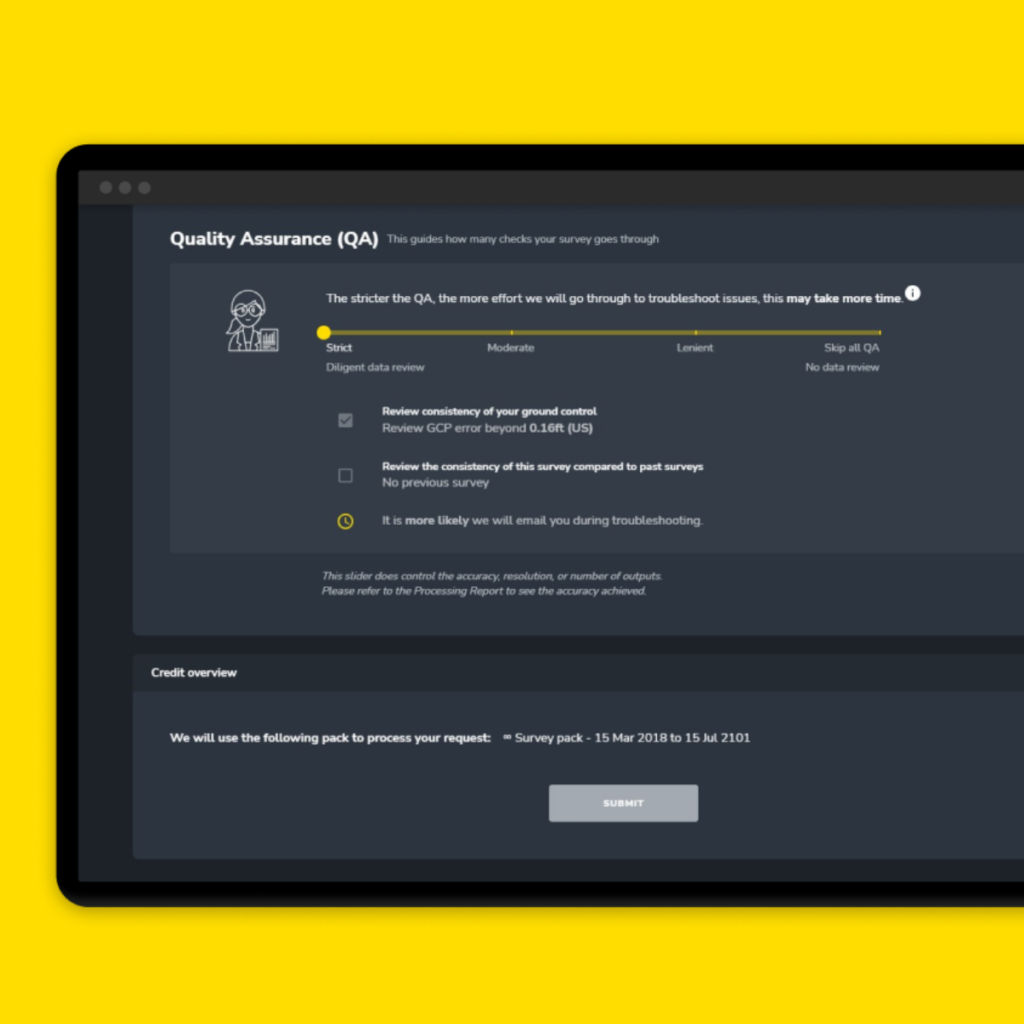
Processing PPK surveys through Propeller is:
Propeller’s data processing cycle
What you do:
01
02
03
What we do:
Create the 3D model
Complete the georeferencing
Validate the data
Create the site’s orthophoto
Check the model’s accuracy
A note about accuracy
It takes a lot of technical expertise to turn millions of data points into realistic and accurate 3D maps. Our survey processing pipeline is managed by a team of geospatial scientists, making accuracy repeatable and predictable, no matter how many datasets you’re juggling.
With Propeller’s outsourced solution, you’re done as soon as you upload your data. We’ll build a high-resolution terrain model, point cloud, orthophoto, and other survey deliverables in a matter of hours. We work as an extension of your survey team, using a mix of automated QA and human supervision to ensure historical consistency between datasets.
Here’s a sample processing report if you’d like to dig into the accuracy.
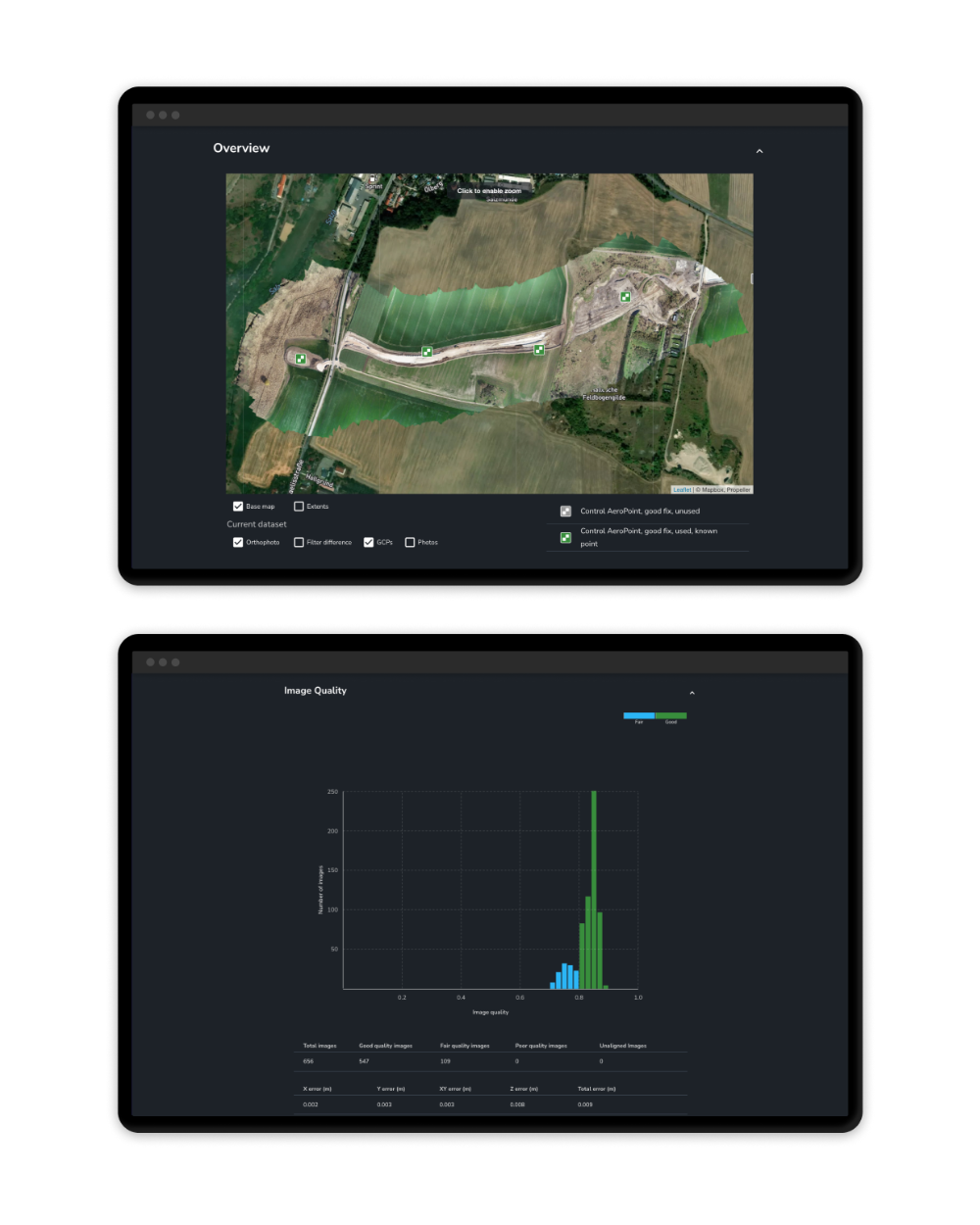
How can PPK transform your worksite?
How PPK can transform your business
Speed
Reliability
Scalability
How to get started with drones
- Assess your budget and surveying requirements: The right drone hardware for you depends on your budget and the needs of your worksite(s). Establish clear parameters for your drone surveying program as a first step.
- Get licensed: Licensing requirements for commercial drone pilots vary by country, so check for details on the licensing requirements where you operate.
- Contact Propeller for support: We’re here to make Propeller PPK easy to implement, so reach out to our team early with any questions you have about how to get started.
How to upgrade your existing drone fleet to PPK
- Check compatibility: Make sure your current fleet is PPK-compatible by using our supported drones tool, or follow our guide to purchase a recommended drone.
- Buy at least one AeroPoint: Get started with smart ground control using AeroPoints. As a combined GCP and base unit, you can survey using just one AeroPoint for a 100-acre site. Use additional AeroPoints as validation checkpoints.
All your FAQs, answered.
PPK stands for “post-processing kinematic.” PPK is a type of drone surveying workflow that improves the accuracy of location data. Unlike traditional surveying techniques, PPK leverages GPS data post-flight to enhance the accuracy of your location tags. When you survey using PPK drone mapping, the images and GPS data collected by your drone are corrected against data from a base station after you fly instead of in real-time.
The difference between PPK (post-processing kinematic) and RTK (real-time kinematic) workflows is how base station data is processed for correction and accuracy.
In a PPK workflow, the drone associates X, Y, and Z coordinates with each image based on its onboard GPS unit. While this is happening, a base unit (this could be a base station, an AeroPoint, or CORS network) also records positional information, but with much more accurate triangulation.
After the flight is over, the two sets of GPS data are matched together using image timestamps. The drone’s onboard GPS data is corrected by the more accurate base unit, providing precise geotags for image data after the fact and survey data that’s accurate within 1/10ft (3cm).
Real-time might sound like the best option, but it actually introduces the opportunity for error. To achieve data accuracy, the RTK drone must stay connected to the base station during flight. If the drone and base station lose connectivity for even a moment, your overall survey accuracy is compromised. This can happen for lots of reasons: antenna orientation, unreliable signal, disruption from rugged terrain or other visual barriers, and even the natural movement of the drone. All of this introduces a margin of error.
We know how important accuracy and reliability are to our customers, and Propeller PPK is the most accurate and reliable start-to-finish drone surveying and data processing solution.
An RTK correction method needs to maintain a constant connection to a base station during the entire duration of a flight to collect data successfully, which means that even a slight signal loss (like flying behind a building) creates big problems.
PPK does not require this constant contact, making it a much better solution for most worksites and use cases.
However, Propeller does offer support for RTK correction workflows with high-accuracy geotags. Check with a sales representative or get in touch here to see if your existing hardware is compatible.